Stop Wasting Money on Preventable Operational Problems
Hospitals lose millions yearly to inefficient scheduling, supply waste, and poor resource allocation. Fix these costly problems before they impact your bottom line and patient care.
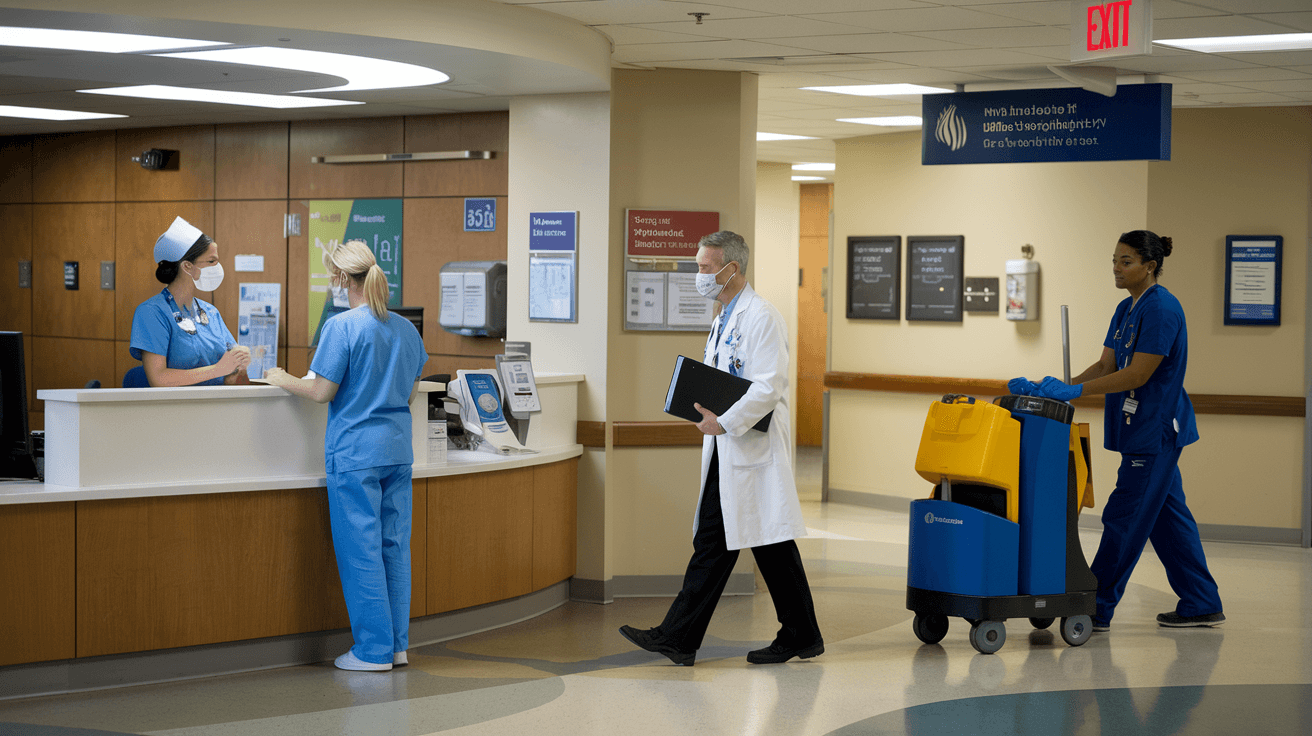
Market Context: The Evolving Hospital Operations Landscape
Hospitals face a fundamental challenge: operating costs keep rising while reimbursements shrink. Most waste money on preventable operational problems - overstocked supplies that expire, underutilized equipment, and inefficient staff scheduling that leads to overtime costs.
The Supply Chain Crisis
Hospitals throw away £3.2M in expired supplies annually per facility. 42% of these losses are preventable through better inventory tracking and demand prediction.
Resource Utilization Problems
The average hospital owns £12M in mobile equipment but can only locate 42% of it when needed. Staff waste 4,000 hours annually searching for equipment.
Scheduling Inefficiency
Poor staff scheduling costs hospitals £800K annually per 100 beds in unnecessary overtime. 76% of schedule gaps could be prevented with better planning.
The Challenge: Industry Pain Points
Hospital administrators face constant pressure to cut costs without impacting care quality. Most current systems force them to choose between efficiency and effectiveness - leading to waste in both time and resources.
Supply Chain Waste
Hospitals overstock to avoid shortages, leading to expired supplies. Meanwhile, critical items still run out because usage patterns aren't properly tracked or predicted.
Equipment Management
Valuable equipment sits unused in some departments while others waste time searching for available units. No one has a real-time view of what's available where.
Staff Scheduling
Managers spend 12+ hours weekly creating schedules that still result in coverage gaps and overtime. Last-minute changes create a cascade of staffing problems.
Cost Visibility
Department managers can't see how their decisions affect costs until monthly reports arrive - too late to prevent waste or adjust operations.
These operational inefficiencies directly affect the bottom line. The average 250-bed hospital loses £7.2M annually to preventable operational problems.
The Perceptura Solution: Transforming Hospital Operations
We help hospitals track and optimize their operations in real time, catching wasteful patterns before they become expensive problems.
Supply Chain Optimization
Stop throwing away expired supplies while preventing stockouts.
- Real-time inventory tracking
- Usage pattern prediction
- Automated reorder optimization
- Expiration date management
Resource Management
Know where everything is and how it's being used.
- Equipment location tracking
- Utilization monitoring
- Preventive maintenance scheduling
- Cross-department sharing
Staff Scheduling
Build better schedules that prevent overtime costs.
- Patient demand prediction
- Skills-based scheduling
- Real-time gap detection
- Overtime prevention
Technical Implementation
We integrate with your existing hospital systems - ERP, scheduling software, and asset management tools. The system begins identifying saving opportunities immediately while learning your specific operational patterns.
Implementation Approach
Most hospitals see initial cost savings within the first month, starting with supply chain optimization and scheduling improvements.
Business Impact: Measurable Results
Hospitals using this approach have achieved significant operational savings without compromising care quality:
Long-Term Benefits
- Lower operating costs
- Better resource utilization
- Reduced staff frustration
- Improved care delivery
- Greater cost visibility
Transform Your Hospital Operations Operations with Perceptura
Join industry leaders who have revolutionized their approach to hospital operations with our AI-driven solutions.
Optimize Your Hospital Operations